5 Tips to Keep Your Roller Chain Working
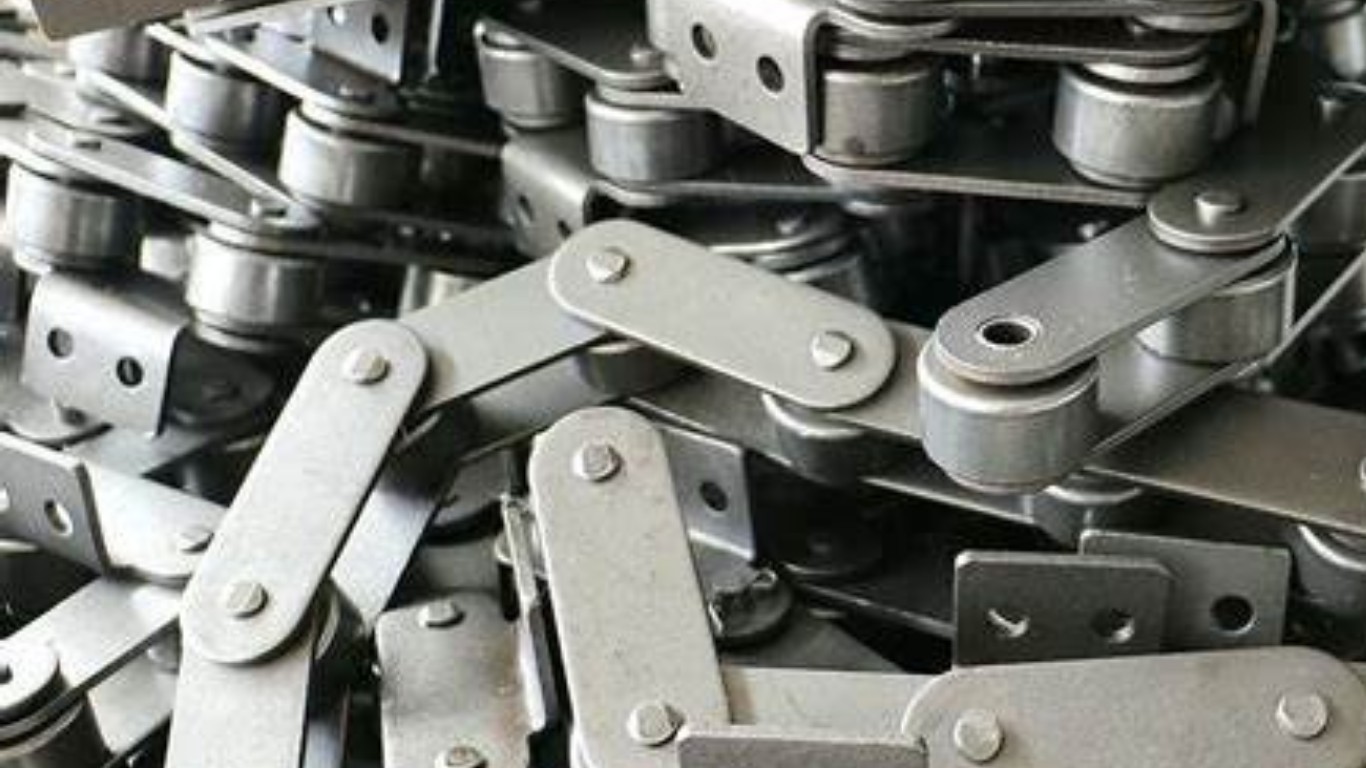
Today, roller chains drive countless power transmission and conveyor applications. Even so, roller chain maintenance is critical to maximizing its service life and efficiency–especially in construction and mining applications where high profile and strict safety guidelines are required. Here are some tips to make sure your device keeps scrolling smoothly.
1. Follow the maintenance schedule.
Roller chains in conveyors (and their sprockets) require regular inspection and maintenance. Periodically perform maintenance checks on them to ensure they are properly tensioned, lubricated, and aligned. In a properly sized and installed drive, the roller chain is expected to last approximately 15,000 hours.
Smaller tasks such as chain adjustments, oil, and filter changes should be scheduled every three months, while larger tasks - such as cleaning components, aligning shafts, re-lubricating the entire machine, replacing or repairing wear and damage of side plates and sprockets, as well as unblocking blocked feed pipes - should be done annually.
Adherence to maintenance schedules is especially important when roller chains are working in mining and construction. Without regular service, heavy machinery can break down and cause injury, not to mention project delays.
Tip: A comprehensive maintenance plan helps project managers clearly outline what needs to be done and when. Most of the items that need to be addressed can be easily adjusted and maintained when done on a regular basis and will preserve the life of the machine and the safety of the workers.
2. Choose lubricating oil and lubrication method wisely.
Roller chains and drives are generally made of stainless steel, and protection from dust and moisture ensures they run smoothly.
Most require a high-quality, non-cleaning petroleum-based oil. Avoid heavy oils and greases as they are usually too hard to get into the chain work surface. There are many ways to lubricate a roller chain, including:
• Manual lubrication
• Spot lubrication
• Disc lubrication
• Flow lubrication
Which is the best? It depends on the chain speed and power delivered by the equipment.
Tip: Proper lubrication of the roller chain is critical. It reduces wear and provides other benefits, such as heat dissipation. A good lubricant can also cushion shock loads.
3. Look for a chain with a properly heat-treated sub-assembly.
Mechanical components can be improved and degraded by heat treatment. Therefore, in order to work effectively, the manufacturer must precisely control this treatment of any part in order for it to function. In other words, proper heat treatment is critical to extending wear life, but if not done properly, it can cause more harm than good.
Two key elements of heat transfer in parts are surface depth and surface hardness. These must be within the bounds of maximizing durability and resistance. When the depth of surface hardness is too deep, the part can become brittle and fall off during operation.
4. Ensure proper tension and alignment.
The chain tension in the slack span should be continuously checked and maintained to see if it needs adjustment. If the tension exceeds the available adjustment, remove both pitches and reconnect the chain. However, if the wear exceeds the functional limit or is greater than 3% (0.36 in/ft), the entire chain must be replaced.
A new chain should not be attached to a worn chain as it will roughen up and damage the drive. If the chain wears more than this 3%, it should not continue to operate. That's because if it's still running, the damage will spread to the roller chain sprocket.
Any noticeable wear on the inner surfaces of the roller chainplates is caused by misaligned sprockets. But regular inspection of the sprockets can prevent additional abnormal sprocket and chain wear.
5. Get hardened parts to prevent wear and failure.
For most machinery in the construction and mining industries, the main disadvantage of roller chains is chain and sprocket wear. This is the main cause of chain stretch, which eventually leads to failure, requiring a complete chain and sprocket replacement.
To solve this problem, solid roller chains are manufactured using parts with high surface hardness. This significantly improves wear resistance, extends service life, and improves performance in harsh environments. If you need to buy a high-quality roller chain, welcome to contact us.
ZMIE is a professional custom transmission chains supplier. Since 2003, ZMIE has exhibited high-quality roller chains, forged chains, conveyor chains, welded steel chains, closed track chains, sprockets, components, and more. We focus on sustainable and long-term relationships with our clients. And support world-renowned brands that put customer privacy and growth first.